Hydraulic System S

The Hydraulic System S is a powerful and versatile tool in the world of engineering, offering efficient and precise control over various mechanical systems. In this comprehensive guide, we will delve into the intricacies of this system, exploring its components, functions, and applications. By the end of this article, you'll have a deep understanding of how Hydraulic System S works and its impact on modern machinery.
Understanding Hydraulic System S

Hydraulic System S is a sophisticated system that utilizes fluid power to transmit and control energy. It operates on the principle of Pascal's law, which states that a change in pressure at any point in an enclosed fluid system is transmitted undiminished to all points in the system.
This system consists of several key components working together to achieve precise and efficient motion control. Here's a breakdown of these components:
Fluid Reservoir
The fluid reservoir, often referred to as the hydraulic tank, serves as the storage unit for the hydraulic fluid. It provides a consistent supply of fluid to the system, ensuring smooth operation. The reservoir also helps regulate the temperature of the fluid, preventing overheating and maintaining optimal performance.
Pump
The pump is the heart of the Hydraulic System S. It generates the necessary pressure by converting mechanical energy into hydraulic energy. There are various types of pumps used in hydraulic systems, including gear pumps, piston pumps, and vane pumps. Each type has its own advantages and is suited for specific applications.
Valves
Valves are crucial components that control the flow and direction of hydraulic fluid within the system. They allow for precise manipulation of the fluid, enabling the system to perform specific actions. Common types of valves used in Hydraulic System S include directional control valves, pressure control valves, and flow control valves.
Actuators
Actuators are the components that convert hydraulic energy into mechanical motion. They come in various forms, such as hydraulic cylinders and hydraulic motors. Hydraulic cylinders provide linear motion, making them ideal for tasks like lifting, pushing, and pulling. Hydraulic motors, on the other hand, generate rotary motion, making them suitable for applications like powering hydraulic pumps or driving rotating machinery.
Hoses and Tubes
Hoses and tubes are essential for connecting the different components of the Hydraulic System S. They transport hydraulic fluid between the reservoir, pump, valves, and actuators. These hoses and tubes are designed to withstand high pressure and temperature, ensuring reliable and safe operation.
Applications of Hydraulic System S

The versatility of Hydraulic System S makes it a popular choice in various industries. Here are some key applications where this system excels:
Construction Equipment
Hydraulic System S plays a vital role in construction machinery, such as excavators, bulldozers, and cranes. The precise control and high power-to-weight ratio of hydraulic systems make them ideal for lifting heavy loads, digging, and performing intricate movements required in construction projects.
Manufacturing and Automation
In manufacturing, Hydraulic System S is used in a wide range of applications, including press machines, material handling equipment, and assembly lines. The system's ability to provide precise control and high force makes it an essential component in automated production processes.
Agriculture
Agricultural machinery, such as tractors, harvesters, and irrigation systems, relies on Hydraulic System S for efficient and reliable operation. Hydraulic systems enable farmers to control the movement of heavy equipment, adjust settings, and perform various agricultural tasks with ease.
Transportation
The transportation industry benefits greatly from Hydraulic System S. It is used in braking systems, suspension systems, and steering mechanisms in vehicles, ensuring smooth and responsive control. Additionally, hydraulic systems are crucial in heavy-duty vehicles like buses and trucks, providing the necessary power and control for safe and efficient operation.
Aerospace
Hydraulic System S is an integral part of the aerospace industry. It is used in aircraft landing gear, flight control surfaces, and hydraulic actuators. The system's ability to provide precise and reliable control under extreme conditions makes it indispensable in aerospace applications.
Benefits of Hydraulic System S

The adoption of Hydraulic System S offers numerous advantages across various industries. Here are some key benefits:
- Power and Efficiency: Hydraulic systems can generate high power with relatively compact components, making them efficient and space-saving.
- Precision Control: The precise control offered by hydraulic systems allows for accurate and repeatable movements, ensuring consistent performance.
- Versatility: Hydraulic System S can be adapted to a wide range of applications, from heavy-duty construction equipment to delicate manufacturing processes.
- Reliability: With proper maintenance, hydraulic systems can provide reliable and long-lasting performance, reducing downtime and maintenance costs.
- Safety: Hydraulic systems are designed with safety in mind, incorporating features like pressure relief valves and emergency shut-off systems to prevent accidents.
Maintenance and Troubleshooting

To ensure the optimal performance and longevity of Hydraulic System S, regular maintenance and troubleshooting are essential. Here are some key maintenance practices and common issues to watch out for:
Maintenance Practices
- Regularly inspect and clean the hydraulic fluid reservoir to prevent contamination.
- Change the hydraulic fluid as recommended by the manufacturer to maintain optimal viscosity and performance.
- Inspect hoses, tubes, and connections for leaks or damage, and replace them if necessary.
- Monitor the performance of pumps, valves, and actuators, and replace or repair them as needed.
- Keep the system well-lubricated to prevent friction and wear.
Common Issues and Troubleshooting
- Leakage: Inspect all connections and components for leaks. Tighten or replace seals and gaskets as necessary.
- Low Pressure: Check for blocked filters, worn-out pumps, or air in the system. Ensure proper maintenance and replace faulty components.
- Contaminated Fluid: Inspect the fluid for contamination and change it if necessary. Regularly clean the reservoir and filters to prevent contamination.
- Stuck Valves: Inspect valve mechanisms for debris or foreign objects. Clean or replace valves as needed.
- Actuator Malfunction: Check for hydraulic fluid leaks, worn-out seals, or damaged actuator components. Replace or repair the actuator as required.
Conclusion
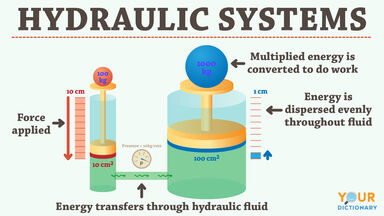
Hydraulic System S is a powerful and versatile tool that has revolutionized various industries, offering precise control and efficient performance. From construction equipment to aerospace applications, this system has proven its reliability and adaptability. By understanding its components, functions, and applications, engineers and technicians can harness the full potential of Hydraulic System S to drive innovation and efficiency in their respective fields.
What are the key advantages of using Hydraulic System S over other power transmission systems?
+Hydraulic System S offers several advantages over other power transmission systems. Firstly, it provides a high power-to-weight ratio, allowing for compact and efficient designs. Secondly, the system’s ability to transmit power over long distances and around corners makes it versatile and adaptable. Additionally, Hydraulic System S offers precise control, ensuring accurate and repeatable movements. Lastly, the system’s reliability and safety features make it a preferred choice in critical applications.
Can Hydraulic System S be used in delicate applications, such as medical equipment or robotics?
+Absolutely! Hydraulic System S is highly adaptable and can be customized for delicate applications. By using precise control valves and sensitive actuators, the system can provide the necessary precision and force for medical equipment, robotics, and other precision-oriented applications. The system’s ability to handle high pressures and provide smooth, controlled movements makes it an excellent choice for such applications.
What are some common challenges when implementing Hydraulic System S, and how can they be overcome?
+One common challenge is the potential for fluid contamination, which can lead to system failure. Regular maintenance, proper filtration, and the use of high-quality hydraulic fluid can help prevent contamination. Another challenge is the need for precise component sizing and calibration to ensure optimal performance. Consulting with experienced engineers and following manufacturer guidelines can help overcome these challenges and ensure successful implementation.
Are there any environmental considerations when using Hydraulic System S?
+Yes, environmental considerations are important when using Hydraulic System S. Proper handling and disposal of hydraulic fluid are crucial to prevent environmental contamination. Additionally, the system’s energy efficiency and the use of biodegradable fluids can help reduce the environmental impact. It’s essential to follow local regulations and guidelines for the safe and sustainable use of hydraulic systems.
How can I ensure the safety of personnel working with Hydraulic System S?
+Safety should be a top priority when working with Hydraulic System S. Proper training and adherence to safety protocols are essential. Regular maintenance and inspection of the system can help identify potential hazards and prevent accidents. Additionally, the use of safety devices, such as pressure relief valves and emergency shut-off systems, can provide an extra layer of protection for personnel.